Bundesgerichtshof Urteil, 18. Apr. 2019 - X ZR 61/17


Gericht
Richter
BUNDESGERICHTSHOF
Der X. Zivilsenat des Bundesgerichtshofs hat auf die mündliche Verhandlung vom 18. April 2019 durch die Richter Dr. Bacher, Dr. Grabinski und Hoffmann sowie die Richterinnen Dr. Kober-Dehm und Dr. Marx
für Recht erkannt:
4. Überwachungssystem nach einem der Ansprüche 1 bis 3, dadurch gekennzeichnet, dass das Überwachungssystem für jede Überwachungsaufgabe an den Komponenten von Werkzeugmaschinen einen oder mehrere zusätzliche Sensoren aufweist, auf die das Überwachungssystem automatisch umschaltet, wenn der entsprechende Überwachungsabschnitt für die Überwachungsaufgabe an Komponenten von Werkzeugmaschinen von der Maschinensteuerung aufgerufen wird. 5. Überwachungssystem nach Anspruch 1, dadurch gekennzeichnet, dass zur Überwachung von Schäden oder Verschleiß an den Vorschubschlitten - Kraftsensoren zur Erfassung der Vorschubkraft in Schlittenbewegungsrichtung an einem der Vorschubspindellagerböcke, - Strom- oder Leistungssensoren an den Vorschubspindelmotoren oder - für eine Überwachung von Geräuschen oder Schwingungen an Vorschubschlitten ein oder mehrere Körperschallsensoren und/oder Schwingungssensoren auf den Schlitten, den Führungsbahnen und/oder den Spindellagerböcken angeordnet sind. 6. Überwachungssystem nach Anspruch 1, dadurch gekennzeichnet, dass die Überwachung von Schäden oder Verschleiß an den Vorschubschlitten durch Auslesen der Messwerte der vorhandenen Stromsensoren an den Vorschubantrieben aus der Maschinensteuerung über die bidirektionale Schnittstelle erfolgt. 7. Verfahren zur prozessbegleitenden Überwachung von Werkzeugmaschinen -Komponenten mit einem Überwachungssystem nach Anspruch 1, in dem - Messsignale aus dem Bearbeitungsprozess, die mindestens einer Kraftrichtung, einer Kraftresultierenden, einem Druck, einem Drehmoment, einer Motorleistung, einem Motorstrom, einer Schwingung, einer Beschleunigung, einem Körperschallgeräusch oder einer Abstandsänderung zwischen zwei Maschinenbauteilen gleichzusetzen sind, von mindestens einem Sensor erfasst werden, - Überwachungsdaten in werkzeug- oder schnittspezifischen Überwachungsabschnitten von mindestens einer Überwachungshardware mit Software gespeichert und verglichen werden , wobei die Überwachungsabschnitte von der Maschinensteuerung durch das NC- und/oder SPS-Programm über eine Schnittstelle vorgegeben werden und wobei in den Überwachungsabschnitten ein Vergleich der Messsignale oder Messsignalkurven von mindestens einem Sensor mit gespeicherten Überwachungsschwellen durch Überwachungs- und Auswertestrategien erfolgt, derart, dass bei Messsignalen, die die Überwachungsschwellen verletzen, eine entsprechende Meldung an die Maschinensteuerung zur entsprechenden Reaktion der Maschine gegeben wird, - ein Datenaustausch zwischen der Maschine und dem Überwachungssystem über eine bidirektionale Schnittstelle vorgenommen wird, wobei die werkzeug- oder schnittspezifischen Überwachungsabschnitte in Form von Datenworten als unterschiedliche Nummern oder Befehle, vorzugsweise als Werkzeugcode, Werkzeugkorrektur- oder Platznummern, Schnittcode oder Hoder M-Befehle, aus dem NC- bzw. SPS-Programm an das Überwachungssystem zwecks Aufteilung der Überwachung in verschiedene Überwachungsabschnitte geleitet werden, dadurch gekennzeichnet, dass in anderen Überwachungsabschnitten, die zu Zeiten, in denen kein Bearbeitungsprozess stattfindet, von der Maschinensteuerung vorgegeben werden, Schäden oder Verschleiß an den Vorschubschlitten von dem Überwachungssystem erkannt, überwacht oder zielgerichtet überprüft werden, wobei die Maschinensteuerung in der Zeit, in der sie den Überwachungsabschnitt zur Überprüfung von Vorschubschlitten an das Überwachungssystem vorgibt, auch den oder die Vorschubschlitten über die zu überprüfenden Verfahrbereiche , vorzugsweise über die gesamten Verfahrbereiche, bewegt , ohne dabei einen Bearbeitungsprozess auszuführen, und sie diese Bewegungen über einen NC-Unterprogrammteil ausführen kann, der zusammen mit dem Datenwort für den Überwachungsabschnitt aufgerufen wird. 8. Verfahren nach Anspruch 7, dadurch gekennzeichnet, dass die Maschinensteuerung den Überwachungsabschnitt zur Überprüfung von Vorschubschlitten dann ausführt, wenn sich kein Werkstück in der Maschine befindet, so dass ohne Kollisionsgefahr und ohne Bearbeitungsprozess die gesamten Verfahrbereiche bewegt bzw. hin und her bewegt werden können. 9. Verfahren nach Anspruch 7, dadurch gekennzeichnet, dass insbesondere in der Massenfertigung von Werkstücken die Maschinensteuerung für den Überwachungsabschnitt zur Überprüfung von Vorschubschlitten das normale NC-Programm zur Bearbeitung dieses Werkstückes mit ihren Vorschubschlitten durchfährt, jedoch dazu kein Werkstück in die Maschine einlegt und anstelle der Überwachungsabschnitte zur Überwachung von Werkzeugen, Werkstücken oder Bearbeitungsprozessen in diesem Fall den Überwachungsabschnitt zur Überwachung von Vorschubschlitten an das Überwachungssystem leitet.
10. Verfahren nach Anspruch 7 bis 9, dadurch gekennzeichnet, dass während des Aufrufens des Überwachungsabschnittes die Bewegung des Vorschubschlittens stets identisch ist und der Überwachungszyklus in regelmäßigen zeitlichen Abständen durch die Maschinensteuerung bei identischen Betriebsbedingungen der Werkzeugmaschine wiederholt ausgelöst wird. 11. Verfahren nach Anspruch 7 bis 10, dadurch gekennzeichnet, dass der Überwachungsabschnitt zur zielgerichteten Überprüfung von Vorschubschlitten von der Maschinensteuerung praktisch unbegrenzt oft innerhalb der Lebensdauer einer Werkzeugmaschine vorgegeben werden kann. 12. Verfahren nach Anspruch 11, dadurch gekennzeichnet, dass der zeitliche Abstand zwischen jeweils zwei gleichen Überwachungsabschnitten zur zielgerichteten Überprüfung von Vorschubschlitten von der Maschinensteuerung so vorgegeben ist, wie eine gerade noch wahrnehmbare, verschleißbedingte Änderung an den Führungsbahnen zeitlich zu erwarten wäre. 13. Verfahren nach Anspruch 7 bis 12, dadurch gekennzeichnet, dass bei neuen bzw. einwandfreien, unverschlissenen Vorschubschlitten ein Teach-In-Überwachungsabschnitt durchgeführt wird, bei dem die Messsignale bzw. Messsignalkurven der Sensoren im Überwachungssystem abgespeichert und in Relation dazu die Schaltschwellen bzw. Schaltschwellenkurven für die maximal zulässigen Abweichungen der Sensorsignale für die künftigen Überwachungsabschnitte bis zum Ende der Lebensdauer der Vorschubschlitten der Werkzeugmaschine festgelegt werden. 14. Verfahren nach Anspruch 7 bis 13, dadurch gekennzeichnet, dass die Messsignale bzw. Messsignalkurven der Sensoren aus den aufeinander folgenden, gleichen Überwachungsabschnitten zur Überprüfung der Vorschubschlitten im Überwachungssystem abgespeichert und jederzeit ausgelesen werden können. 15. Verfahren nach Anspruch 7 bis 14, dadurch gekennzeichnet, dass nach einer Maschinenkollision oder einem Werkzeugbruch, wie es das Überwachungssystem standardmäßig feststellen kann und an die Maschinensteuerung meldet, die Maschinensteuerung nach Bereinigung der Kollisions- oder Bruchsituation mit Beginn der regulären Bearbeitung im Automatikbetrieb zunächst einen im Hinblick auf die sonst übliche zeitliche Abfolge außerplanmäßigen Überwachungsabschnitt zur zielgerichteten Überprüfung der Vorschubschlitten ausführt und dass das Überwachungssystem die Messsignale bzw. Messsignalkurven der Sensoren in diesem Fall separat abspeichert, um eventuelle Schäden durch die Kollision oder den Werkzeugbruch an den Vorschubschlitten zu dokumentieren. 16. Verfahren zur prozessbegleitenden Überwachung von Werkzeugmaschinen -Komponenten mit einem Überwachungssystem nach Anspruch 2, in dem - Messsignale aus dem Bearbeitungsprozess, die mindestens einer Kraftrichtung, einer Kraftresultierenden, einem Druck, einem Drehmoment, einer Motorleistung, einem Motorstrom, einer Schwingung, einer Beschleunigung, einem Körperschallgeräusch oder einer Abstandsänderung zwischen zwei Maschinenbauteilen gleichzusetzen sind, von mindestens einem Sensor erfasst werden, - Überwachungsdaten in werkzeug- oder schnittspezifischen Überwachungsabschnitten von mindestens einer Überwachungshardware mit Software gespeichert und verglichen werden , wobei die Überwachungsabschnitte von der Maschinensteuerung durch das NC- und/oder SPS-Programm über eine Schnittstelle vorgegeben werden und wobei in den Überwa- chungsabschnitten ein Vergleich der Messsignale oder Messsignalkurven von mindestens einem Sensor mit gespeicherten Überwachungsschwellen durch Überwachungs- und Auswertestrategien erfolgt, derart, dass bei Messsignalen, die die Überwachungsschwellen verletzen, eine entsprechende Meldung an die Maschinensteuerung zur entsprechenden Reaktion der Maschine gegeben wird, - ein Datenaustausch zwischen der Maschine und dem Überwachungssystem über eine bidirektionale Schnittstelle vorgenommen wird, wobei die werkzeug- oder schnittspezifischen Überwachungsabschnitte in Form von Datenworten als unterschiedliche Nummern oder Befehle, vorzugsweise als Werkzeugcode, Werkzeugkorrektur- oder Platznummern, Schnittcode oder Hoder M-Befehle, aus dem NC- bzw. SPS-Programm an das Überwachungssystem zwecks Aufteilung der Überwachung in verschiedene Überwachungsabschnitte geleitet werden, dadurch gekennzeichnet, dass in anderen Überwachungsabschnitten, die zu Zeiten, in denen kein Bearbeitungsprozess stattfindet, von der Maschinensteuerung vorgegeben werden, Schäden oder Verschleiß an den Werkzeugoder Werkstückspindeln von dem Überwachungssystem erkannt, überwacht oder zielgerichtet überprüft werden, wobei zur Überwachung von Schäden bzw. Verschleiß an Werkzeug- oder Werkstückspindeln , vorrangig an deren Lagern, sowie zur Überprüfung von unzulässiger Unwucht an Werkzeug- oder Werkstückspindeln diese über Körperschallsensoren zur Erfassung des Laufgeräusches bzw. über Schwingungssensoren zur Erfassung von Spindelschwingungen bzw. über Abstandssensoren zur Erfassung von Verlagerungen zwischen zwei Spindelbauteilen, bevorzugt von Rotor und Stator zueinander bzw. über Temperatursensoren zur Erfas- sung verlustleistungsbedingter Temperaturerhöhungen jeweils im unmittelbaren Bereich der Lagerungen bzw. über Strom- oder Leistungssensoren am Werkzeug- oder Werkstückspindelmotor, auch durch Auslesen der Messwerte der vorhandenen Stromsensoren an den Spindelantrieben aus der Maschinensteuerung über die bidirektionale Schnittstelle zur Erfassung verlustleistungsbedingter Stromoder Leistungserhöhungen verfügen, wobei die Maschinensteuerung in der Zeit, in der sie den Überwachungsabschnitt zur Überprüfung von Werkzeug- oder Werkstückspindeln an das Überwachungssystem vorgibt, auch die Spindeln in die zu überprüfenden Drehzahlbereiche steuert, vorzugsweise diese über ihren gesamten Drehzahlbereich rauf- und runterfährt, ohne dabei einen Bearbeitungsprozess auszuführen, und sie das Ansteuern der Spindeln über einen NC-Unterprogrammteil ausführen kann, der zusammen mit dem Datenwort für den Überwachungsabschnitt aufgerufen wird. 17. Verfahren nach Anspruch 16, dadurch gekennzeichnet, dass die Maschinensteuerung den Überwachungsabschnitt zur Überprüfung von Werkzeugspindeln dann ausführt, wenn sich kein Werkzeug in der Maschine befindet, so dass die Messsignale nicht durch das Werkzeug verfälscht werden können. 18. Verfahren nach Anspruch 16, dadurch gekennzeichnet, dass die Maschinensteuerung den Überwachungsabschnitt zur Überprüfung von Werkstückspindeln dann ausführt, wenn sich kein Werkstück in der Maschine befindet und das Werkstückfutter identisch positioniert ist, so dass die Messsignale nicht durch das Werkstück oder das Werkstückfutter verfälscht werden können. 19. Verfahren nach Anspruch 16 bis 18, dadurch gekennzeichnet, dass während des Aufrufens der jeweiligen Überwachungsabschnitte für die Überprüfung der Werkzeug- oder Werkstückspindeln die jewei- ligen Drehzahlverläufe einschließlich der Beschleunigungs- und Abbremsphasen stets identisch sind und die jeweiligen Überwachungszyklen für die entsprechenden Werkzeug- oder Werkstückspindeln in regelmäßigen zeitlichen Abständen durch die Maschinensteuerung bei identischen Betriebsbedingungen der Werkzeugmaschine wiederholt ausgelöst werden. 20. Verfahren nach Anspruch 16 bis 19, dadurch gekennzeichnet, dass die Überwachungsabschnitte zur zielgerichteten Überprüfung von Werkzeug- oder Werkstückspindeln von der Maschinensteuerung praktisch unbegrenzt oft innerhalb der Lebensdauer einer Werkzeugmaschine vorgegeben werden können. 21. Verfahren nach Anspruch 20, dadurch gekennzeichnet, dass der zeitliche Abstand zwischen jeweils zwei gleichen Überwachungsabschnitten zur zielgerichteten Überprüfung von Werkzeug- oder Werkstückspindeln von der Maschinensteuerung so vorgegeben ist, wie eine gerade noch wahrnehmbare, verschleißbedingte Änderung an den Werkzeug- oder Werkstückspindeln zeitlich zu erwarten wäre. 22. Verfahren nach Anspruch 16 bis 21, dadurch gekennzeichnet, dass bei neuen bzw. einwandfreien, unverschlissenen Werkzeug- oder Werkstückspindeln jeweils ein Teach-In-Überwachungsabschnitt durchgeführt wird, bei dem die Messsignale bzw. Messsignalkurven der Sensoren im Überwachungssystem abgespeichert und in Relation dazu die Schaltschwellen bzw. Schaltschwellenkurven für die maximal zulässigen Abweichungen der Sensorsignale für die künftigen Überwachungsabschnitte bis zum Ende der Lebensdauer der Werkzeug- oder Werkstückspindeln in der Werkzeugmaschine festgelegt werden. 23. Verfahren nach Anspruch 16 bis 22, dadurch gekennzeichnet, dass die Messsignale bzw. Messsignalkurven der Sensoren aus den aufeinanderfolgenden gleichen Überwachungsabschnitten zur Überprüfung von Werkzeug- oder Werkstückspindeln im Überwachungssystem abgespeichert und jederzeit ausgelesen werden können. 24. Verfahren nach Anspruch 16 bis 22, dadurch gekennzeichnet, dass nach einer Maschinenkollision oder einem Werkzeugbruch, wie es das Überwachungssystem standardmäßig feststellen kann und an die Maschinensteuerung meldet, die Maschinensteuerung nach Bereinigung der Kollisions- oder Bruchsituation mit Beginn der regulären Bearbeitung im Automatikbetrieb zunächst einen im Hinblick auf die sonst übliche zeitliche Abfolge außerplanmäßigen Überwachungsabschnitt zur zielgerichteten Überprüfung der Werkzeugoder Werkstückspindeln ausführt und dass das Überwachungssystem die Messsignale bzw. Messsignalkurven der Sensoren in diesem Fall separat abspeichert, um eventuelle Schäden durch die Kollision oder den Werkzeugbruch an den Werkzeug- oder Werkstückspindeln zu dokumentieren. 25. Verfahren nach Anspruch 16, dadurch gekennzeichnet, dass insbesondere in der Massenfertigung von Werkstücken die Maschinensteuerung zur Überprüfung von Werkzeug- oder Werkstückspindeln auf Schäden bzw. Verschleiß das normale NC-Programm zur Bearbeitung dieses Werkstückes durchfährt, jedoch jeweils einen spezifischen Überwachungsabschnitt zur Überwachung der Werkzeugoder Werkstückspindeln auf Schäden bzw. Verschleiß beim jeweiligen Hochlaufen der Spindel vor dem Bearbeitungsprozess mit dem jeweiligen Werkzeug oder Werkstück auf die jeweilige Solldrehzahl zusätzlich zu den normalen Überwachungszyklen zur Überwachung von Werkzeugen, Werkstücken oder Bearbeitungsprozessen an das Überwachungssystem leitet und dabei die Messsignale in der Hochlaufphase der Spindel vorzugsweise durch Schwellen von Signalmusterkurven aus einem entsprechenden Teach-In Überwachungsabschnitt überprüft. 26. Verfahren nach Anspruch 25, dadurch gekennzeichnet, dass die entsprechende Überprüfung auch beim Runterlaufen der Spindel möglich ist. 27. Verfahren nach Anspruch 25 oder 26, dadurch gekennzeichnet, dass die entsprechende Überprüfung der Werkzeug- oder Werkstückspindeln auf Schäden bzw. Verschleiß nur durch Überprüfung der Messsignalwerte innerhalb eines kurzen Zeitfensters während des Hoch- oder Runterlaufens der Spindel erfolgt und hierfür von der Maschinensteuerung ein entsprechend kurzer Überwachungsabschnitt an die Überwachungsvorrichtung geleitet wird. 28. Verfahren zur prozessbegleitenden Überwachung von Werkzeugmaschinen -Komponenten mit einem Überwachungssystem nach Anspruch 3, in dem - Messsignale aus dem Bearbeitungsprozess, die mindestens einer Kraftrichtung, einer Kraftresultierenden, einem Druck, einem Drehmoment, einer Motorleistung, einem Motorstrom, einer Schwingung, einer Beschleunigung, einem Körperschallgeräusch oder einer Abstandsänderung zwischen zwei Maschinenbauteilen gleichzusetzen sind, von mindestens einem Sensor erfasst werden, - Überwachungsdaten in werkzeug- oder schnittspezifischen Überwachungsabschnitten von mindestens einer Überwachungshardware mit Software gespeichert und verglichen werden , wobei die Überwachungsabschnitte von der Maschinensteuerung durch das NC- und/oder SPS-Programm über eine Schnittstelle vorgegeben werden und wobei in den Überwachungsabschnitten ein Vergleich der Messsignale oder Mess- signalkurven von mindestens einem Sensor mit gespeicherten Überwachungsschwellen durch Überwachungs- und Auswertestrategien erfolgt, derart, dass bei Messsignalen, die die Überwachungsschwellen verletzen, eine entsprechende Meldung an die Maschinensteuerung zur entsprechenden Reaktion der Maschine gegeben wird, - ein Datenaustausch zwischen der Maschine und dem Überwachungssystem über eine bidirektionale Schnittstelle vorgenommen wird, wobei die werkzeug- oder schnittspezifischen Überwachungsabschnitte in Form von Datenworten als unterschiedliche Nummern oder Befehle, vorzugsweise als Werkzeugcode, Werkzeugkorrektur- oder Platznummern, Schnittcode oder Hoder M-Befehle, aus dem NC- bzw. SPS-Programm an das Überwachungssystem zwecks Aufteilung der Überwachung in verschiedene Überwachungsabschnitte geleitet werden, dadurch gekennzeichnet, dass in anderen Überwachungsabschnitten, die zu Zeiten, in denen kein Bearbeitungsprozess stattfindet, von der Maschinensteuerung vorgegeben werden, fehlerhafte Zustände an Komponenten von Werkzeugmaschinen von dem Überwachungssystem erkannt, überwacht oder zielgerichtet überprüft werden, wobei zur Überwachung von Schäden oder Verschleiß an sonstigen motorbetriebenen Vorrichtungen der Maschine, wie Hydraulikaggregat, Kühlschmiermittelpumpe , Antrieb der Schutztür etc., im folgenden Aggregate genannt, Messsignale von Strom- oder Leistungssensoren an den Antriebsmotoren bzw. für eine Überwachung von Geräuschen oder Schwingungen an den Aggregaten Geräusche und Schwingungen an einem oder mehreren Körperschallsensoren und/oder Schwingungssensoren erfasst werden, wobei die Maschinensteuerung in der Zeit, in der sie den Überwachungsabschnitt zur Überprüfung von Aggregaten an das Überwachungssystem vorgibt, auch die entsprechenden Aggregate über die zu überprüfenden Leistungsbereiche, vorzugsweise über die gesamten Leistungsbereiche betreibt bzw. hin und her bewegt, ohne dabei einen Bearbeitungsprozess auszuführen, und sie diese Bewegungen über einen NC-Unterprogrammteil ausführen kann, der zusammen mit dem Datenwort für den Überwachungsabschnitt aufgerufen wird. 29. Verfahren nach Anspruch 28, dadurch gekennzeichnet, dass die Maschinensteuerung den Überwachungsabschnitt zur Überprüfung von Aggregaten dann ausführt, wenn sich kein Werkstück in der Maschine befindet, so dass ohne Kollisionsgefahr und ohne Bearbeitungsprozess die Aggregate in ihrem gesamten Leistungsbereich betrieben bzw. hin und her bewegt werden können. 30. Verfahren nach Anspruch 28 bis 29, dadurch gekennzeichnet, dass der Überwachungsabschnitt zur zielgerichteten Überprüfung von Aggregaten von der Maschinensteuerung praktisch unbegrenzt oft innerhalb der Lebensdauer einer Werkzeugmaschine vorgegeben werden kann. 31. Verfahren nach Anspruch 30, dadurch gekennzeichnet, dass der zeitliche Abstand zwischen jeweils zwei gleichen Überwachungsabschnitten zur zielgerichteten Überprüfung von Aggregaten von der Maschinensteuerung so vorgegeben ist, wie eine gerade noch wahrnehmbare, verschleißbedingte Änderung an den Aggregaten zeitlich zu erwarten wäre. 32. Verfahren nach Anspruch 28 bis 31, dadurch gekennzeichnet, dass bei neuen bzw. einwandfreien, unverschlissenen Aggregaten ein Teach-In-Überwachungsabschnitt durchgeführt wird, bei dem die Messsignale bzw. Messsignalkurven der Sensoren im Überwachungssystem abgespeichert und in Relation dazu die Schaltschwellen bzw. Schaltschwellenkurven für die maximal zulässigen Abweichungen der Sensorsignale für die künftigen Überwachungsabschnitte bis zum Ende der Lebensdauer der Aggregate der Werkzeugmaschine festgelegt werden. 33. Verfahren nach Anspruch 28 bis 32, dadurch gekennzeichnet, dass die Messsignale bzw. Messsignalkurven der Sensoren aus den aufeinanderfolgenden gleichen Überwachungsabschnitten zur Überprüfung der Aggregate im Überwachungssystem abgespeichert und jederzeit ausgelesen werden können. Die Kosten des Rechtsstreits werden gegeneinander aufgehoben.
Von Rechts wegen
Tatbestand:
Der Beklagte war Inhaber des am 10. September 2002 unter Inan1 spruchnahme der Priorität einer deutschen Patentanmeldung vom 10. September 2001 angemeldeten und mit Wirkung für die Bundesrepublik Deutschland erteilten europäischen Patents 1 425 640 (Streitpatents), das ein System und ein Verfahren zur prozessbegleitenden Überwachung von Werkzeugen , Werkstücken oder Bearbeitungsprozessen in spanabhebenden Werkzeugmaschinen betrifft. Die Streithelferin, die dem Rechtsstreit in erster Instanz auf Seiten der Beklagten beigetreten ist, ist seit dem 25. August 2016 eingetragene Inhaberin des Streitpatents.
Patentanspruch 1, auf den die Patentansprüche 2 bis 5 unmittelbar oder
- 2
- mittelbar rückbezogen sind, und Patentanspruch 6, auf den die Patentansprüche 7 bis 45 unmittelbar oder mittelbar rückbezogen sind, haben in der erteilten Fassung folgenden Wortlaut: "1. Überwachungssystem zur prozessbegleitenden Überwachung von Werkzeugen, Werkstücken oder Bearbeitungsprozessen in spanabhebenden Werkzeugmaschinen zum Drehen, Bohren oder Fräsen mit dem Ziel der Erkennung von mindestens einem der Zustände Werkzeugbruch, Werkzeugausbruch, Werkzeugverschleiß, Werkzeug -zu-Werkstückkontakt mit oder ohne Werkstückmaßkontrolle, Maschinenkollisionen oder Prozessentartungen wie Rattern, werkzeug -, werkstück- oder schnittspezifische Überlast oder Unterlast, bestehend aus - mindestens einem Sensor zur Erfassung von Messsignalen aus dem Bearbeitungsprozess, die mindestens einer Kraftrichtung, einer Kraftresultierenden, einem Druck, einem Drehmoment, einer Motorleistung, einem Motorstrom, einer Schwingung, einer Beschleunigung, einem Körperschallgeräusch oder einer Abstandsänderung zwischen zwei Maschinenbauteilen gleichzusetzen sind, - mindestens einer Überwachungshardware mit Software zur Speicherung und zum Vergleich von Überwachungsdaten in Werkzeug- oder schnittspezifischen Überwachungsabschnitten, die von der Maschinensteuerung durch das NC- und/oder SPSProgramm über eine Schnittstelle vorgegebenen werden und in denen ein Vergleich der Messsignale oder Messsignalkurven von mindestens einem Sensor mit gespeicherten Überwachungsschwellen durch Überwachungs- und Auswertestrategien erfolgt, derart, dass bei Messsignalen, die die Überwachungsschwellen verletzen, eine entsprechende Meldung an die Maschinensteuerung zur entsprechenden Reaktion der Maschine gegeben wird, - mindestens einer bidirektionalen Schnittstelle, vorzugsweise einer Feldbusschnittstelle, zwischen der Überwachungshardware und der Maschinensteuerung, wobei die bidirektionale Schnittstelle einen Datenaustausch zwischen der Maschine und dem Überwachungssystem vornimmt und insbesondere dazu geeignet ist, die werkzeug- oder schnittspezifischen Überwachungsabschnitte , in Form von Datenworten als unterschiedliche Nummern oder Befehle, vorzugsweise als Werkzeugcode, Werkzeugkorrektur - oder Platznummern, Schnittcode, H- oder M-Befehle, aus dem NC- bzw. SPS-Programm an das Überwachungssystem zwecks Aufteilung der Überwachung in verschiedene Überwachungsabschnitte zu leiten, - und vorzugsweise einer Bedienungshardware mit Software zur Bedienung und/oder Parametrierung des Überwachungssystems und/oder zur Visualisierung der Messsignale, dadurch gekennzeichnet, dass das Überwachungssystem in anderen Überwachungsabschnitten , die zu Zeiten, in denen kein Bearbeitungsprozess stattfindet, von der Maschinensteuerung vorgegeben werden, fehlerhafte Zustände an Komponenten von Werkzeugmaschinen, vorzugsweise Schäden oder Verschleiß an den Vorschubschlitten oder an den Werkzeug- oder Werkstückspindeln erkennt, überwacht oder zielgerichtet überprüft. 6. Verfahren zur prozessbegleitenden Überwachung von Werkzeugmaschinen -Komponenten mit einem Überwachungssystem nach einem der Ansprüche 1 bis 5 in dem - Messsignale aus dem Bearbeitungsprozess, die mindestens einer Kraftrichtung, einer Kraftresultierenden, einem Druck, einem Drehmoment, einer Motorleistung, einem Motorstrom, einer Schwingung, einer Beschleunigung, einem Körperschallgeräusch oder einer Abstandsänderung zwischen zwei Maschinenbauteilen gleichzusetzen sind, von mindestens einem Sensor erfasst werden, - Überwachungsdaten in werkzeug- oder schnittspezifischen Überwachungsabschnitten von mindestens einer Überwachungshardware mit Software gespeichert und verglichen werden , wobei die Überwachungsabschnitte von der Maschinensteuerung durch das NC- und/oder SPS-Programm über eine Schnittstelle vorgegeben werden und wobei in den Überwachungsabschnitten ein Vergleich der Messsignale oder Messsignalkurven von mindestens einem Sensor mit gespeicherten Überwachungsschwellen durch Überwachungs- und Auswer- testrategien erfolgt, derart, dass bei Messsignalen, die die Überwachungsschwellen verletzen, eine entsprechende Meldung an die Maschinensteuerung zur entsprechenden Reaktion der Maschine gegeben wird, - ein Datenaustausch zwischen der Maschine und dem Überwachungssystem über eine bidirektionale Schnittstelle vorgenommen wird wobei die werkzeug- oder schnittspezifischen Überwachungsabschnitte in Form von Datenworten als unterschiedliche Nummern oder Befehle, vorzugsweise als Werkzeugcode, Werkzeugkorrektur - oder Platznummern, Schnittcode oder H- oder MBefehle , aus dem NC- bzw. SPS-Programm an das Überwachungssystem zwecks Aufteilung der Überwachung in verschiedene Überwachungsabschnitte geleitet werden, dadurch gekennzeichnet, dass in anderen Überwachungsabschnitten, die zu Zeiten in denen kein Bearbeitungsprozess stattfindet von der Maschinensteuerung vorgegeben, fehlerhafte Zustände an Komponenten von Werkzeugmaschinen , vorzugsweise Schäden oder Verschleiß an den Vorschubschlitten oder an den Werkzeug- oder Werkstückspindeln von dem Überwachungssystem erkannt, überwacht oder zielgerichtet überprüft werden." Die Klägerin hat geltend gemacht, der Gegenstand des Streitpatents sei
- 3
- nicht neu und beruhe nicht auf einer erfinderischen Tätigkeit. Die Erfindung sei auch nicht so deutlich und vollständig offenbart, dass ein Fachmann sie ausführen könne. Zudem sei der Gegenstand von Patentanspruch 6 unzulässig erweitert. Die Beklagte hat das Streitpatent im Hauptantrag wie erteilt und in der Fassung von zuletzt vier Hilfsanträgen beschränkt verteidigt. Das Patentgericht hat das Streitpatent für nichtig erklärt. Mit ihrer Berufung verteidigt die Beklagte das Streitpatent im Hauptantrag
- 4
- zuletzt noch in der Fassung des in der ersten Instanz gestellten ersten Hilfsantrags sowie hilfsweise mit den weiteren drei dort gestellten Hilfsanträgen. Die Klägerin tritt dem Rechtsmittel entgegen.
Entscheidungsgründe:
- 5
- Die Berufung der Beklagten ist zulässig und hat im Umfang des Hauptantrags , mit dem die Beklagte das Streitpatent noch verteidigt, auch in der Sache Erfolg.
- 6
- I. Das Streitpatent betrifft ein System und ein Verfahren zur prozessbegleitenden Überwachung von Werkzeugen, Werkstücken oder Bearbeitungsprozessen in spanabhebenden Werkzeugmaschinen.
- 7
- 1. In der Streitpatentschrift wird ausgeführt, dass Komponenten von Werkzeugmaschinen überwachungsbedürftig seien, die einem Verschleiß unterliegen oder die aufgrund von Maschinenkollisionen, Maschinenüberlastungen oder unwuchten Werkzeugen oder Werkstücken beschädigt werden könnten.
- 8
- zur prozessbegleitenden Überwachung von Werkzeugen, Werkstücken oder Bearbeitungsprozessen in spanabhebenden Werkzeugmaschinen zum Drehen, Bohren oder Fräsen bekannt. Diese hätten das Ziel, mindestens einen der Zustände Werkzeugbruch, Werkzeugausbruch, Werkzeugverschleiß, Werkzeugzu -Werkstückkontakt, Rattern oder Maschinenkollisionen "in-process" zu erkennen und insbesondere bei Werkzeugbruch oder Maschinenkollisionen die Maschinenantriebe so schnell wie möglich still zu setzen, um Folgeschäden zu vermeiden. Solche "In-Prozess"-Überwachungssysteme verfügten bereits über eine
- 9
- Schnittstelle zwischen dem Überwachungssystem und der Maschinensteuerung , um in von der Steuerung vorgegebenen Überwachungsabschnitten die Signalverläufe der Sensoren während des Prozesses zu überwachen und die Maschinen gegebenenfalls über dieselbe Schnittstelle stillzusetzen. Dabei wür- den zunehmend Feldbusschnittstellen anstelle von parallelen Schnittstellen zum Informationsaustausch zwischen dem Überwachungssystem und der Maschinensteuerung , bestehend aus der speicherprogrammierbaren Steuerung (SPS) bzw. der NC-Steuerung, verwendet. Es sei auch ein Verfahren bekannt, mit dem auf Basis von Messdaten
- 10
- mindestens eines Vibrationssensors eine "Post-process"-Überprüfung stattfinde , um fehlerhafte Zustände an Werkzeugmaschinenkomponenten nachträglich zu charakterisieren.
- 11
- 2. Der Erfindung liegt nach den Angaben der Streitpatentschrift die Aufgabe zugrunde, ein Überwachungssystem und ein Verfahren zur prozessbegleitenden Überwachung von Werkzeugmaschinenkomponenten zu schaffen, die ohne nennenswerte Änderungen an der Hard- oder Software des Überwachungssystems Komponenten von Werkzeugmaschinen überwachen und überprüfen können.
- 12
- - X ZR 128/09, GRUR 2015, 356 Rn. 9 - Repaglinid) ist das der Erfindung zugrundeliegende technische Problem darin zu sehen, ein System und ein Verfahren zu entwickeln, das mit möglichst geringem Aufwand eine prozessbegleitende Überwachung von Werkzeugmaschinenkomponenten ermöglicht.
- 13
- 3. Das soll nach Patentansprüchen 1, 2 und 3 in der zuletzt im Hauptantrag verteidigten Fassung durch drei Systeme erreicht werden, die jeweils die Merkmale 1 bis 1.4.1 umfassen, an die sich nach Patentanspruch 1 die Merkmale 1.4.21 und 7, nach Patentanspruch 2 die Merkmale 1.4.22, 16 und 17 sowie nach Patentanspruch 3 die Merkmale 1.4.23, 39 und 40 anschließen: Patentansprüche 1, 2 und 3: 1. Überwachungssystem 1.1 zur prozessbegleitenden Überwachung von Werkzeugen, Werkstücken oder Bearbeitungsprozessen in spanabhebenden Werkzeugmaschinen zum Drehen, Bohren oder Fräsen 1.2 mit dem Ziel der Erkennung von mindestens einem der Zustände Werkzeugbruch, Werkzeugausbruch, Werkzeugverschleiß, Werkzeug -zu-Werkstückkontakt mit oder ohne Werkstückmaßkontrolle, Maschinenkollisionen oder Prozessentartungen wie Rattern, werkzeug -, werkstück- oder schnittspezifische Überlast oder Unterlast, 1.3 bestehend aus jeweils mindestens 1.3.1 einem Sensor zur Erfassung von Messsignalen aus dem Bearbeitungsprozess, 1.3.1.1 die mindestens einer Kraftrichtung, einer Kraftresultierenden , einem Druck, einem Drehmoment, einer Motorleistung, einem Motorstrom, einer Schwingung , einer Beschleunigung, einem Körperschallgeräusch oder einer Abstandsänderung zwischen zwei Maschinenbauteilen gleichzusetzen sind, 1.3.2 einer Überwachungshardware mit Software zur Speicherung und zum Vergleich von Überwachungsdaten in werkzeugoder schnittspezifischen Überwachungsabschnitten, 1.3.2.1 die von der Maschinensteuerung durch das NCund / oder SPS-Programm über eine Schnittstelle vorgegeben werden und 1.3.2.2 in denen ein Vergleich der Messsignale oder Messsignalkurven von mindestens einem Sensor mit gespeicherten Überwachungsschwellen durch Überwachungs - und Auswertestrategien erfolgt, 1.3.2.3 derart, dass bei Messsignalen, die die Überwachungsschwellen verletzen, eine entsprechende Meldung an die Maschinensteuerung zur entsprechenden Reaktion der Maschine gegeben wird, 1.3.3 einer bidirektionalen Schnittstelle, vorzugsweise einer Feldbusschnittstelle , zwischen der Überwachungshardware und der Maschinensteuerung, 1.3.3.1 wobei die bidirektionale Schnittstelle einen Datenaustausch zwischen der Maschine und dem Überwachungssystem vornimmt und 1.3.3.2 insbesondere dazu geeignet ist, die werkzeug- oder schnittspezifischen Überwachungsabschnitte, in Form von Datenworten als unterschiedliche Nummern oder Befehle, vorzugsweise als Werkzeugcode , Werkzeugkorrektur- oder Platznummern, Schnittcode, H- oder M-Befehle, aus dem NC- bzw. SPS-Programm an das Überwachungssystem zwecks Aufteilung der Überwachung in verschiedene Überwachungsabschnitte zu leiten, 1.3.4 und vorzugsweise einer Bedienungshardware mit Software zur Bedienung und/oder Parametrierung des Überwachungssystems und/oder zur Visualisierung der Messsignale ; 1.4 in anderen Überwachungsabschnitten, 1.4.1 die zu Zeiten, in denen kein Bearbeitungsprozess stattfindet, von der Maschinensteuerung vorgegeben werden, Nur Patentanspruch 1: 1.4.21 erkennt, überwacht oder überprüft das Überwachungssystem zielgerichtet Schäden oder Verschleiß an den Vorschubschlitten. 7. Die Maschinensteuerung bewegt in der Zeit, in der sie den Überwachungsabschnitt zur Überprüfung von Vorschubschlitten an das Überwachungssystem vorgibt, auch den oder die Vorschubschlitten über die zu überprüfenden Verfahrbereiche , vorzugsweise über die gesamten Verfahrbereiche , ohne dabei einen Bearbeitungsprozess auszuführen, bewegt und sie [die Maschinensteuerung] diese Bewegungen über einen NC-Unterprogrammteil ausführen kann, der zusammen mit dem Datenwort für den Überwachungsabschnitt aufgerufen wird. Nur Patentanspruch 2: 1.4.22 erkennt, überwacht oder überprüft das Überwachungssystem zielgerichtet Schäden oder Verschleiß an den Werkzeug - oder Werkstückspindeln. 16. Zur Überwachung von Schäden bzw. Verschleiß an Werkzeug - oder Werkstückspindeln, vorrangig an deren Lagern, sowie zur Überprüfung von unzulässiger Unwucht an Werkzeug - oder Werkstückspindeln verfügen diese über Körperschallsensoren zur Erfassung des Laufgeräusches bzw. über Schwingungssensoren zur Erfassung von Spindelschwingungen bzw. über Abstandssensoren zur Erfassung von Verlagerungen zwischen zwei Spindelbauteilen, bevorzugt von Rotor und Stator zueinander bzw. über Temperatursensoren zur Erfassung verlustleistungsbedingter Temperaturerhöhungen jeweils im unmittelbaren Bereich der Lagerungen bzw. über Strom- oder Leistungssensoren am Werkzeugoder Werkstückspindelmotor, auch durch Auslesen der Messwerte der vorhandenen Stromsensoren an den Spindelantrieben aus der Maschinensteuerung über die bidirektionale Schnittstelle zur Erfassung verlustleistungsbedingter Strom- oder Leistungserhöhungen. 17. In der Zeit, in der die Maschinensteuerung den Überwachungsabschnitt zur Überprüfung von Werkzeug- oder Werkzeugspindeln an das Überwachungssystem vorgibt, steuert sie [die Maschinensteuerung] auch die Spindeln in die zu überprüfenden Drehzahlbereiche, fährt vorzugsweise diese über ihren gesamten Drehzahlbereich rauf- und runter, ohne dabei einen Bearbeitungsprozess auszuführen und kann sie [die Maschinensteuerung] das Ansteuern der Spindeln über einen NC-Unterprogrammteil ausführen, der zusammen mit dem Datenwort für den Überwachungsabschnitt aufrufen wird. Nur Patentanspruch 3: 1.4.23 erkennt, überwacht oder überprüft das Überwachungssystem zielgerichtet fehlerhafte Zustände an Komponenten von Werkzeugmaschinen. 39. Zur Überwachung von Schäden bzw. Verschleiß an sonstigen motorbetriebenen Vorrichtungen der Maschine, wie Hydraulikaggregat , Kühlschmiermittelpumpe, Antrieb der Schutztür etc., im folgenden Aggregate genannt, werden Messsignale von Strom- oder Leistungssensoren an den Antriebsmotoren bzw. für eine Überwachung von Geräuschen oder Schwingungen an den Aggregaten, Geräusche und Schwingungen an einen oder mehrere Körperschallsensoren und/oder Schwingungssensoren erfasst. 40. In der Zeit, in der die Maschinensteuerung den Überwachungsabschnitt zur Überprüfung von Aggregaten an das Überwachungssystem vorgibt, betreibt sie [die Maschinensteuerung ] auch die entsprechenden Aggregate über die zu überprüfenden Leistungsbereiche bzw. bewegt diese hin und her, vorzugsweise über die gesamten Leistungsbereiche, ohne dabei einen Bearbeitungsprozess auszuführen und kann sie [die Maschinensteuerung] diese Bewegungen über einen NC-Unterprogrammteil ausführen, das zusammen mit dem Datenwort für den Überwachungsabschnitt aufgerufen wird.
- 14
- 4. Die Lehre der Patentansprüche 1, 2 und 3 des Streitpatents ist aus Sicht des Fachmanns, den das Patentgericht zutreffend in einem Ingenieur (Diplom-Ingenieur oder Ingenieur mit Master-Abschluss) im Fachbereich Maschinenbau mit mehrjähriger Erfahrung auf dem Gebiet der Entwicklung von Überwachungssystemen für industrielle Fertigungsmaschinen, wie insbesondere Werkzeugmaschinen, gesehen hat, wie folgt weiter zu erläutern:
- 15
- a) Das erfindungsgemäße System ist für die Überwachung von Werkzeugen, Werkstücken oder Bearbeitungsprozessen in spanabhebenden Werkzeugmaschinen auf im Einzelnen genannte fehlerhafte Zustände vorgesehen (Merkmale 1.1 und 1.2) und umfasst mindestens einen Sensor, der geeignet ist, Messsignale aus dem Bearbeitungsprozess zu erfassen (Merkmal 1.3.1), eine Überwachungshardware mit Software, die geeignet sind, Überwachungsdaten in werkzeug- oder schnittspezifischen Überwachungsabschnitten zu speichern und zu vergleichen (Merkmal 1.3.2), und eine bidirektionale Schnittstelle zwischen der Überwachungshardware und der Maschinensteuerung (Merkmal 1.3.3).
- 16
- b) Die Überwachungshardware speichert die von dem Sensor aus dem Bearbeitungsprozess erfassten Messdaten oder Messsignalkurven und vergleicht diese in werkzeug- oder schnittspezifischen Überwachungsabschnitten , die von der Maschinensteuerung durch das NC- und/oder SPS-Programm über die Schnittstelle zwischen der Maschinensteuerung und der Überwachungshardware vorgegeben werden, mit gespeicherten Überwachungsschwellen nach Überwachungs- und Auswertestrategien. Ergibt sich aus dem Vergleich , dass die Messsignale die Überwachungsschwellen verletzen, wird eine Meldung an die Maschinensteuerung gegeben, um eine entsprechende Reaktion der Maschine zu erwirken.
- 17
- c) Das Überwachungssystem hat neben der prozessbegleitenden Überwachung von Werkzeugen und dergleichen die weitere Funktion, Schäden oder Verschleiß an Vorschubschlitten (Merkmal 1.4.21) oder an Werkzeug- oder Werkstückspindeln (Merkmal 1.4.22) oder fehlerhafte Zustände an Komponenten von Werkzeugmaschinen (Merkmal1.4.23) zu erkennen, zu überwachen oder zielgerichtet zu überprüfen. Die Kombination beider Überwachungsfunktionen hat nach der Beschreibung den Vorteil, dass diese mit derselben Überwachungshardware und derselben Schnittstelle verwirklicht werden können. Zudem bedarf es zusätzlicher Sensoren an den Werkzeugkomponenten nur inso- weit, als diese nicht schon für die prozessbegleitende Überwachung erforderlich sind (vgl. Abs. 12 f.).
- 18
- d) Um diese "Synergieeffekte" zu ermöglichen, soll die Überwachung der jeweiligen Werkzeugmaschinenkomponenten durch das Überwachungssystem nach Merkmal 1.4 in "anderen Überwachungsabschnitten" als den Abschnitten stattfinden, in denen die prozessbegleitende Überwachung erfolgt. Als Unterscheidungskriterium sieht Merkmal 1.4.1 vor, dass die Maschinensteuerung die maschinenbezogene Überwachung nur zu Zeiten vorgeben darf, in denen kein Bearbeitungsprozess stattfindet. Entsprechend den Erläuterungen in der Beschreibung, in denen zwischen prozessbegleitender und maschinenbezogener Überwachung unterschieden wird (Abs. 12), sind demnach mit dem Begriff "andere Überwachungsabschnitte" die Zeitabschnitte gemeint, in denen die Werkzeugmaschine nicht spanabhebend tätig ist.
- 20
- e) Im Rahmen der Lehre aus Patentanspruch 2, die die Überwachung oder zielgerichtete Überprüfung auf Schäden oder Verschleiß an den Werkzeug- oder Werkstückspindeln betrifft (Merkmal 1.4.23), ist in Merkmal 17 zusätzlich vorgesehen, dass die Maschinensteuerung in der Zeit, in der sie den Überwachungsabschnitt zur Überprüfung der Werkzeug- oder Werkstückspindeln an das Überwachungssystem vorgibt, auch die Spindeln in die zu überprüfenden Drehzahlbereiche steuert, ohne dabei einen Bearbeitungsprozess auszuführen. Danach genügt es für die Verwirklichung der Lehre aus Patentanspruch 2 nicht, wenn die Steuerung die spindelbezogene Überwachung - entsprechend Merkmal 1.4.1 - in einem Zeitabschnitt vorgibt, in dem keine spanabhebende Bearbeitung des Werkstücks erfolgt, also etwa bei dem zum Zwecke der Bearbeitung ohnehin vorgesehenen Hoch- oder Runterlaufen der Spindel. Vielmehr ist kumulativ erforderlich, dass die Spindeln in zu überprüfende Drehzahlbereiche gesteuert werden können, also auch in Drehzahlbereiche, die für einen gerade anstehenden oder abgeschlossenen Bearbeitungsvorgang nicht erforderlich sind, aber eine maschinenbezogene Überwachung ermöglichen.
- 21
- f) Dieses Verständnis steht nicht in Widerspruch zu den Patentansprüchen 25 und 26 in der zuletzt verteidigten Fassung, die den erteilten Patentansprüchen 26 und 27 entsprechen.
- 22
- aa) Diese Patentansprüche sind für die Auslegung von Patentanspruch 2 von Bedeutung.
- 23
- Patentanspruch 17 entspricht und ein Verfahren schützt. Dessen Merkmale entsprechen aber den funktionsbezogenen Merkmalen von Patentanspruch 2. Das damit beanspruchte Verfahren bildet deshalb zugleich ein Ausführungsbeispiel der Lehre aus Patentanspruch 2. Dieses ist bei der Auslegung zu berücksichtigen , da Patentansprüche im Zweifel so auszulegen sind, dass sämtliche Ausführungsbeispiele zu ihrer Ausfüllung hergezogen werden können (vgl. etwa BGH, Urteil vom 2. Juni 2015 - X ZR 103/13, GRUR 2015, 972 Rn. 13 - Kreuzgestänge
).
- 24
- bb) Auch nach den Patentansprüchen 25 und 26 ist erforderlich, dass zum Zwecke einer maschinenbezogenen Überwachung Drehzahlbereiche angesteuert werden können, die für einen gerade anstehenden oder abgeschlossenen Bearbeitungsvorgang nicht erforderlich sind.
dem Werkzeug oder Werkstück auf die jeweilige Solldrehzahl. Patentanspruch 26 sieht eine entsprechende Möglichkeit beim Runterlaufen der Spindel vor. Zur Verwirklichung dieser zusätzlichen Merkmale genügt es nicht, eine
- 26
- maschinenbezogene Überwachung während des für einen unmittelbar nachfolgenden oder gerade abgeschlossenen Bearbeitungsschritt ohnehin vorgesehenen Beschleunigungsvorgangs der Spindel auszuführen. Vielmehr muss auch hier zusätzlich zu den normalen Überwachungszyklen ein spezifischer Überwachungsabschnitt zur Überwachung der Werkzeug- oder Werkstückspindeln an das Überwachungssystem geleitet werden. Hierzu muss die zu überwachende Spindel, wie sich aus dem Rückbezug auf Patentanspruch 16 ergibt, in zu überprüfende Drehzahlbereiche gesteuert werden können, also in Drehzahlbereiche , die für einen gerade anstehenden oder abgeschlossenen Bearbeitungsvorgang nicht erforderlich sind.
- 27
- g) Entsprechende Anforderungen gelten für die nach Patentanspruch 1 vorgesehene Überwachung des Vorschubschlittens und für die nach Patentanspruch 3 vorgesehene Überwachung von Aggregaten.
- 29
- dafür vorgesehener Steuerbefehle in einem NC-Unterprogrammteil über die zu überprüfenden Leistungsbereiche hin und her bewegt werden können.
- 30
- 5. Für die Auslegung der jeweils ein Verfahren betreffenden Patentansprüche 7, 16 und 28 in der zuletzt verteidigten Fassung gelten die vorstehenden Erläuterungen zu den Patentansprüchen 1, 2 und 3 entsprechend.
- 31
- II. Das Patentgericht hat die Gegenstände der Patentansprüche 1 bis 3 in der zuletzt verteidigten Fassung als nicht auf einer erfinderischen Tätigkeit beruhend angesehen.
- 32
- Druckschrift der A. GmbH aus dem Jahr 2005 (NK5c) bekannt. Die NK5c beschreibe die allgemeine Funktionalität des CTM-Systems der A. GmbH. Die Überwachung des Prozesses leiste eine CTM-Karte, die direkt in einen Bedienrechner der Maschinensteuerung eingesetzt werden könne. Die Verbindung mit der Maschinensteuerung und der Sensorik werde über zwei Busstecker hergestellt. An die CTM-Karte könnten verschiedene Sensoren angeschlossen werden. Jede Sensorik verfüge über einen Messumformer. Die Messumformer wandelten die Messsignale in digitale Daten um, die über einen seriellen Sensorbus zur CTM-Karte gesandt würden, um dort verarbeitet und ausgewertet zu werden. Die CTM-Karte weise einen Anschluss für eine bidirektionale Schnittstelle (Profibus DP) mit der Maschinensteuerung auf. Mittels der CTM-Karte würden Bruch, Verschleiß und Fehlen des Werkzeugs sicher erkannt. Zudem könne durch Überwachung der Schwinggeschwindigkeit am Spindelgehäuse mittels eines Beschleunigungssensors während des Anlaufs, also zu Zeiten, in denen kein Bearbeitungsprozess stattfinde, ein unwuchtes Werkzeug oder ein sich anbahnender Maschinenschaden, beispielsweise am Wälzlager der Hauptspindel, erkannt werden. Das Überwachungssystem sei damit zur prozess - und (in anderen Abschnitten) maschinenbezogenen Überwachung geeignet , wobei für beide dieselbe Hardware verwendet werde. In der NK5c werde weiterhin ausgeführt, dass neben einem unwuchten
- 33
- Werkzeug durch regelmäßige, vergleichende Messungen der Schwinggeschwindigkeit eines für diese Messungen bestimmten Masterwerkzeugs mit dem aktuellen Schwinggeschwindigkeitswert auch sich anbahnende Maschinenschäden , z.B. am Wälzlager der Hauptspindel, erkannt werden könnten. Dadurch werde der Fachmann angeregt, nach Lösungen zu suchen, wie mittels des beschriebenen Überwachungssystems weitere Arten von Maschinenschäden erkannt werden könnten. Infolge dieser Anregung werde er die europäische Patentanmeldung
- 34
- 762 248 (NK9) berücksichtigen, die sich mit der Charakterisierung einer Werkzeugmaschine einschließlich der Maschinenstruktur, des Werkzeugs, der Befestigung , des Werkstücks und der Betriebsumgebung auseinandersetze. In der Entgegenhaltung werde auch ausgeführt, dass die Überwachung erfolgen könne , um die Ursache von verschiedenen Anomalien in bestehenden Maschinen zu erkennen. Die NK9 lehre den Fachmann eine gezielte Anordnung von Beschleunigungs - und Schwingungssensoren an verschiedenen Komponenten der Werkzeugmaschine, um Informationen über Spindellager, Schlitten, Werkstücke , Befestigungen, Maschinenstruktur, Spindelmotoren und Pumpen zu erhalten. Die Signalauswertung könne dazu verwendet werden, Unwucht, Fehlausrichtung , mechanische Lockerheit, Gangdefekte, Lagerdefekte, Rattern, unzureichende Befestigung, Werkzeugprobleme und strukturelle Probleme zu erkennen. Dadurch werde der Fachmann veranlasst, das aus der NK5c bekannte Überwachungssystem für Werkzeugmaschinen derart weiterzubilden, dass auch dieses der Erkennung von Schäden oder Verschleiß an Vorschubschlitten oder anderen Komponenten von Werkzeugmaschinen diene. Aus der NK9 gehe weiterhin hervor, die Maschinenüberwachungen in
- 35
- einem Leerlaufzyklus, in dem "Luft geschnitten" werde, mithin wenn kein Bearbeitungsprozess stattfinde, durchzuführen. Der Fachmann werde dadurch veranlasst , die Maschinensteuerung darauf auszurichten, dass sie in der Zeit, in der sie den Überwachungsabschnitt zur Überprüfung von Vorschubschlitten, Werkzeug- oder Werkstückspindeln und Aggregaten an das Überwachungssystem vorgibt, auch die Vorschubschlitten über die zu überprüfenden Verfahrbereiche bewegt, die Spindeln in die zu überprüfenden Drehzahlbereiche steuert oder die entsprechenden Aggregate über die zu überprüfenden Leistungsbereiche bewegt, ohne dabei einen Bearbeitungsprozess auszuführen. Diese Bewegungen über einen NC-Unterprogrammteil auszuführen, der zusammen mit dem Datenwort für den Überwachungsabschnitt aufgerufen werde, folge für den Fachmann von selbst, da bereits in der NK5c alle Bewegungen von einem NCProgramm durchgeführt würden.
- 36
- III. Die Beurteilung des Patentgerichts hält der Überprüfung im Berufungsverfahren in einem entscheidenden Punkt nicht stand.
- 37
- 1. Soweit die Beklagte das Streitpatent im Berufungsverfahren nicht mehr verteidigt, bleibt es ohne weitere Sachprüfung bei der Nichtigerklärung.
- 38
- 2. Die Verteidigung des Streitpatents in der zuletzt mit dem Hauptantrag verteidigten Fassung ist zulässig.
- 39
- Hauptantrag verteidigten Fassung des Streitpatents nicht entgegen, dass diese aus der Kombination eines Erzeugnisanspruchs (Patentanspruch 1) mit einem oder mehreren Verfahrensansprüchen (Patentansprüche 7; 16 und 17; 39 und 40) hervorgegangen sind. Als Bestandteil eines Erzeugnisanspruchs sind die hinzugefügten Merkmale - ebenso wie die schon nach der erteilten Fassung vorgesehenen Merkmale, die das Verhalten der geschützten Maschine näher beschreiben - so zu verstehen, dass das erfindungsgemäße System objektiv geeignet sein muss, diese auszuführen.
- 40
- 3. Entgegen der Auffassung des Patentgerichts ist dem Fachmann der Gegenstand der Erzeugnisansprüche 1, 2 und 3 sowie der Verfahrensansprüche 7, 16 und 28 durch den Stand der Technik nicht nahegelegt worden.
- 41
- a) Zu Recht ist das Patentgericht allerdings davon ausgegangen, dass die Merkmale 1 bis 1.4.22 dem Fachmann durch die NK5c offenbart worden sind.
- 42
- aa) Das stellt die Berufung hinsichtlich der Offenbarung der Merkmale 1 bis 1.3.4 nicht in Frage. Insoweit kann deshalb auf die zutreffende Begründung des Patentgerichts Bezug genommen werden.
- 43
- bb) Das Patentgericht ist weiterhin zutreffend zu dem Ergebnis gelangt , dass die Merkmale 1.4 bis 1.4.22 aus der NK5c bekannt waren.
- 44
- (1) Die Berufung sieht diese Merkmale als nicht offenbart an, weil eine zeitgleiche Werkzeug- und Maschinenüberwachung durch die erfindungsgemäße Lehre ausgeschlossen werde. In der NK5c werde lediglich offenbart, dass die Schwinggeschwindigkeit am Spindelgehäuse während des Anlaufs überwacht werde. Das sei kein "anderer Überwachungsabschnitt" im Sinne des Merkmals 1.4.
- 45
- (2) Dem kann nicht beigetreten werden.
- 47
- ausgeführt, dass die Überwachung der Schwinggeschwindigkeit am Spindelgehäuse durch einen Beschleunigungs-Sensor mit nachgeschaltetem Messwandler erfolgen kann, so dass ein unwuchtes Werkzeug an einer zu hohen Schwinggeschwindigkeit während des Anlaufs erkannt und über einen Alarm gemeldet werden kann (NK5c S. 12 r. Sp.). Die Überwachung der Spindel kann also von der Steuerung in einem Zeitabschnitt vorgegeben werden, in dem, da die Spindel noch hochläuft, keine spanabhebende Bearbeitung durch die Werkzeugmaschine stattfindet.
- 48
- cc) Nicht zu beanstanden ist auch die Beurteilung des Patentgerichts, dass es in der NK5c an einer Offenbarung des Merkmals 16 fehlt, da die Entgegenhaltung keinen Hinweis darauf enthält, dass die Spindel während des Hochlaufens, wenn kein Bearbeitungsprozess ausgeführt wird, aufgrund entsprechender Steuerbefehle in zu überprüfende Drehzahlbereiche gesteuert wird.
- 49
- Steuern in zu überprüfende Drehzahlbereiche nicht bereits in dem Umstand gesehen werden, dass die Spindel beim Hochlaufen von Null auf die Drehzahl hochläuft, mit der das Werkstück bearbeitet werden soll. Wie oben im Einzelnen dargelegt wurde, ist vielmehr erforderlich, dass auch Drehzahlbereiche angesteuert werden können, die für einen gerade anstehenden oder abgeschlossenen Bearbeitungsvorgang nicht erforderlich sind, aber eine maschinenbezogene Überwachung ermöglichen. Solche Überwachungsabschnitte sind in NK5c nicht offenbart.
- 50
- dd) Ebenfalls nicht in NK5c offenbart sind die Merkmale 1.4.21 und 7 (zielgerichtete Überprüfung der Schäden oder des Verschleißes an den Vorschubschlitten durch Bewegen über zu überprüfende Verfahrbereiche) sowie die Merkmale 1.4.23 und 40 (zielgerichtete Überprüfung auf fehlerhafte Zustände an Komponenten der Werkzeugmaschine durch Bewegen über zu überprüfende Leistungsbereiche).
- 51
- b) Der Gegenstand der Patentansprüche 1, 2 und 3 ergab sich für den Fachmann auch nicht aus der Veröffentlichung von D. L. , in der das System CTM im Rahmen eines Zeitschriftenartikels (MM - Das Industriemagazin 2001, S. 24 ff., NK3) vorgestellt wird. Der Offenbarungsgehalt dieser Veröffentlichung geht nicht über denjenigen der NK5c hinaus.
- 52
- c) Der Fachmann wurde, wie das Patentgericht weiterhin zutreffend ausgeführt hat, durch die NK5c dazu angeregt, nach Lösungen zu suchen, wie das dort beschriebene Überwachungssystem mit zusätzlichen Funktionen ausgestattet werden kann, etwa zur Erkennung von Schäden an anderen Maschinenkomponenten , und dass er Anlass hatte, unter diesem Aspekt die NK9 in den Blick zu nehmen.
- 53
- Werkzeugmaschine, zur Überprüfung einer tatsächlichen Maschinenkonstruktion auf die Einhaltung bestimmter Normen oder zur Identifizierung der Ursachen von Anomalien bei bestehenden Maschinen (NK9 Sp. 2 Z. 18 ff.). Hierzu gehört auch eine Überwachung von Komponenten der Werkzeugmaschine im Bearbeitungsprozess (NK9 Sp. 2 Z. 18 ff.). Diese erfolgt zwar anders als in NK5c nicht im Rahmen einer prozessbegleitenden Überwachung, sondern im Zusammenhang mit einer anlassbezogenen Untersuchung der Maschine. Dennoch hatte der Fachmann Veranlassung, auf der Suche nach zusätzlichen Möglichkeiten zur prozessbegleitenden Überwachung auch solche Überwachungsvorgänge in Betracht zu ziehen. Ungeachtet des unterschiedlichen Anlasses, aus dem die Überwachung erfolgt, weisen die eingesetzten Überwachungsmittel große Ähnlichkeit auf. Vor diesem Hintergrund ergab sich für den Fachmann, der ausgehend
- 54
- von NK5c nach weiteren Möglichkeiten zur prozessbegleitenden Überwachung befand, aus NK9 die Anregung, auch den Vorschubschlitten und andere Aggregate der Werkzeugmaschine während des Hochfahrens zu überwachen.
- 55
- d) Entgegen der Auffassung des Patentgerichts gab die NK9 dem Fachmann aber keine Veranlassung, die aus der NK5c bekannte Überwachung von Maschinenkomponenten derart abzuändern, dass dafür nicht nur das für den Bearbeitungsprozess ohnehin erforderliche Anlaufen der Spindel oder anderer Komponenten genutzt wird, sondern die Spindel oder sonstigen Komponenten während dieses Zeitabschnitts auch gezielt in bestimmte zu überprüfende Drehzahlbereiche gesteuert werden.
- 56
- Die NK9 lehrt zwar, dass die Maschinenüberwachung auch in einem Leerlaufzyklus, "in dem Luft geschnitten wird", erfolgen kann (NK9 Sp. 4 Z. 43 ff.; Z. 58 ff.). Dies wird aber allein in Zusammenhang mit Verfahren zur Maschinencharakterisierung offenbart (NK9 Sp. 4 Z. 1 ff., Sp. 2 Z. 44 ff. i.V.m. dem Flussdiagramm in Figur 1), also für Situationen, in denen die Maschine einer anlassbezogenen besonderen Überprüfung unterzogen wird. Hieraus ergab sich für den Fachmann nicht die Anregung, die in der
- 57
- NK5c offenbarte Überwachung einer Maschinenkomponente in Zusammenhang mit der Durchführung eines Bearbeitungsprozesses mit zusätzlichen, vom Bearbeitungsprozess gelösten Überwachungsabschnitten zu kombinieren, wie sie in NK9 im Mittelpunkt stehen. Die in NK5c offenbarte Lösung mag einen ersten Schritt in diese Richtung darstellen, da sie zusätzlich zu einer Überwachung des Bearbeitungsprozesses die Überwachung einer Maschinenkomponente vorsieht. Weder daraus noch aus den in NK9 offenbarten weiteren Überwachungsmethoden ergab sich aber die Anregung, die für eine prozessbegleitende Überwachung eingesetzten Mittel für Überwachungsabschnitte einzusetzen, die für den Bearbeitungsprozess selbst nicht erforderlich sind, etwa dadurch, dass die Spindel in bestimmte zu überprüfende Drehzahlbereiche gebracht, der Vorschubschlitten über zu überprüfende Verfahrbereiche bewegt oder sonstige Aggregate über zu überprüfende Leistungsbereiche angesteuert werden.
- 58
- e) Fehlt es an einer Anregung für solche Maßnahmen, kann auch die Feststellung des Patentgerichts, dass es sich für den Fachmann ohne weiteres ergebe, die gezielte Steuerung der Spindel über einen NCUnterprogrammteil auszuführen, der zusammen mit dem Datenwort für den Überwachungsabschnitt aufgerufen wird, zu keinem anderen Ergebnis führen.
- 59
- IV. Das Urteil des Patentgerichts stellt sich nicht aus einem anderen Grund als richtig dar.
- 60
- 1. Die Klägerin macht geltend, die Erfindung sei nicht so deutlich und vollständig offenbart, dass ein Fachmann sie ausführen könne, wenn die Lehre der Patentansprüche dahin zu verstehen sei, dass während eines Bearbeitungsprozesses keine maschinenbezogenen Überwachungsvorgänge erfolgen dürften.
- 62
- 2. Entgegen der Auffassung der Klägerin geht der Gegenstand von Patentanspruch 6 nicht über den Inhalt der Ursprungsanmeldung hinaus.
- 64
- V. Die Kostenentscheidung beruht auf § 121 Abs. 2 PatG und §§ 92 Abs. 1, 100 Abs. 1, 101 Abs. 2 ZPO.
Kober-Dehm Marx
Vorinstanz:
Bundespatentgericht, Entscheidung vom 15.02.2017 - 5 Ni 8/15 (EP) -
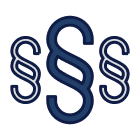
moreResultsText
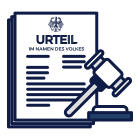
Annotations
(1) In dem Verfahren vor dem Bundesgerichtshof gelten die Bestimmungen des § 144 über die Streitwertfestsetzung entsprechend.
(2) In dem Urteil ist auch über die Kosten des Verfahrens zu entscheiden. Die Vorschriften der Zivilprozeßordnung über die Prozeßkosten (§§ 91 bis 101) sind entsprechend anzuwenden, soweit nicht die Billigkeit eine andere Entscheidung erfordert; die Vorschriften der Zivilprozeßordnung über das Kostenfestsetzungsverfahren (§§ 103 bis 107) und die Zwangsvollstreckung aus Kostenfestsetzungsbeschlüssen (§§ 724 bis 802) sind entsprechend anzuwenden.
(1) Wenn jede Partei teils obsiegt, teils unterliegt, so sind die Kosten gegeneinander aufzuheben oder verhältnismäßig zu teilen. Sind die Kosten gegeneinander aufgehoben, so fallen die Gerichtskosten jeder Partei zur Hälfte zur Last.
(2) Das Gericht kann der einen Partei die gesamten Prozesskosten auferlegen, wenn
- 1.
die Zuvielforderung der anderen Partei verhältnismäßig geringfügig war und keine oder nur geringfügig höhere Kosten veranlasst hat oder - 2.
der Betrag der Forderung der anderen Partei von der Festsetzung durch richterliches Ermessen, von der Ermittlung durch Sachverständige oder von einer gegenseitigen Berechnung abhängig war.